Andersen Sterilizers is pleased to announce its sister company, Andersen Scientific, has been selected by the Food and Drug Administration (FDA) as one of eight international companies it will collaborate with the development of strategies or technologies to reduce ethylene oxide (EO) emissions to as close to zero as possible.
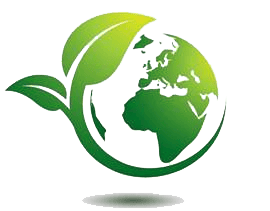
On July 15, 2019, the FDA released two public innovation challenges, “to encourage development of novel sterilization methods.” FDA Innovation Challenge 2, for which Andersen Scientific was selected, is focused on the reduction of EO emissions. According to the FDA, this challenge is, “In response to the February 2019 closure of a large device sterilization facility…”
The FDA announced its list of participants selected for Innovation Challenge 2 on November 25, 2019. Andersen Scientific is one of eight selected from 22 applying companies large and small.
“Collaborating with the FDA Innovation on this challenge is an honor and a natural progression in our decades-long relationship,” said Andersen President and CEO, Ted May. “By expanding the capacity of our exclusive Ethylene Oxide-Flexible Chamber Technology (EO-FCT), we are confident we can significantly enhance the volume of items Scientific processes while reducing emissions even further than our current 99% efficiency.”
“FDA’s choice to partner with Andersen Scientific is reflective of the heavy attention and significant growth our contract sterilization services have received over the past few years,” said Andersen Scientific General Manager, Daryl Woodman. “We perform extensive research and development for clients, as well as commercial sterilization of various lot sizes with incredible gas efficiency and rapid turnaround. Our staff’s entire careers have revolved around solving sterilization problems others couldn’t. This FDA innovation challenge will be no different.”
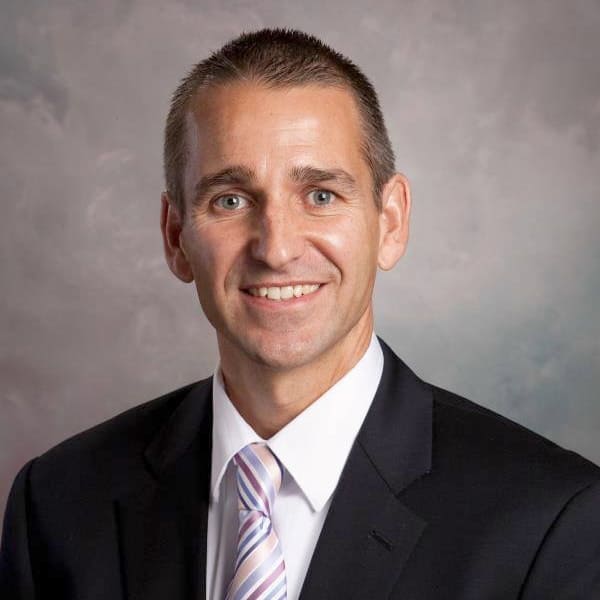
EO-FCT is a non-traditional sterilization process using 100% EO. Unlike traditional EO sterilizers, which involved rigid metal chamber and large external tanks of gas, Andersen Sterilizers’ uses gas impermeable sterilization bags and unit dose 100% EO cartridges. At the start of the cycle, excess air is removed from the bag, eliminating chamber dead space. A tiny fraction of EO is then employed to sterilize. After abatement, emissions are reduced by 99%—effectively zero emissions.
According to the FDA, here’s what happens next.
Participants selected for this challenge will work directly with the FDA to accelerate the development and review of innovative technology.
Within 60 days of announcing the participants, the collaboration phase of the process will begin. The goals of the collaboration phase are to:
- Create a mutual understanding of the target technology profile including the important risks and benefits.
- Discuss the development of the technology or potential regulatory pathways going forward.
The FDA will work closely with the participants selected for the challenges. The regulatory standard of demonstrating a reasonable assurance of safety and effectiveness still applies. Review of these challenge submissions does not constitute regulatory acceptance or endorsement of a process associated with a premarket submission. These methods or technologies would still have to be reviewed through the relevant premarket pathway.